よく使う表面処理の方法はどれらがありますか?それぞれの材料に適した表面処理方法は何がありますか?
発表時間です:
2022-04-06
源:
新民ネット
一、表面の机械的な強化です
工業では、多くの場合、金属表面をクリーンアップ、強化および光整机械処理方法を採用しています。例えば、ジェット処理、ロール加工、内孔押圧、研磨、研磨などです。ジェット処理、研磨処理は生産で広く使われています。
(一)ブラスト処理
ブラスター処理は、高速で噴射した砂丸や鉄丸を利用してワーク表面に強い沖撃を与え、その表面を塑性変形させ、表面を強化し表面の状態を変化させる工法です。ブラストの方法には通常、手作業と機械作業の二つがあります。一般的に使用されるスプレーは、以下のいくつかの種類があります:鋳鉄弾丸、スチール弾丸、ガラス弾丸、砂の弾丸など、黒い金属は鋳鉄弾丸、スチール弾丸、ガラス弾丸を多く使用して、非鉄金属とステンレス鋼は、ガラス弾丸とステンレス弾丸を使用しています。
ブラスト処理は工場で広く採用されている表面強化プロセスで、装置が簡単でコストが安く、工作物の形状や位置に関係なく、操作が容易ですが、作業環境が劣ります。ジェットは、部品の机械強度の向上や耐摩耗性、耐疲労性、耐腐食性の向上などに広く使用されています。表面つや消し、皮酸化除去、鋳・鍛造・溶接の残応力除去などにも使用できます。
(二)磨きと磨きです
研磨研磨は研磨輪で部品表面を加工し、平らで滑らかな研磨面を得る一種の表面処理方法です。部品表面の錆、トラコーマ、溶接スラグ、キズなどの欠陥を取り除き、部品表面の平坦性を向上させます。磨きには粗磨きと細磨きがあります。粗挽きはざらざらした表面や不規則な外形を修正成形することで、手や机械で操作できます。ほとんどの手の操作は非鉄金属に使用されます。机械の操作は鋼材に使用して、普通砥石の上で行います;粗挽きをした後の金属表面の擦れが深いので、細挽きによって消して、研磨の準備をします。細挽きには手挽きと機械挽きがあります。手は細く磨りますから各号の金相砥石の上で行います;よく机械の細かい磨磨机、ワックスの皿、研磨膏の細かい磨プロセスを加速します。研磨用の研磨材を研磨して、青銅、黄銅、鋳鉄、亜鉛などの軟化材料に対して人造金鋼砂を使います;鋼には人造コランダムを使います。金鋼砂はすべての金属の研磨に使用することができて、特に軟靱な金属材料に適します。
ポリッシュは、コーティング層の表面や部品の表面装飾加工の最終工程で、磨き上げ工程後に表面に残る微細な擦れをなくし、光沢のある外観を得ることを目的としています。磨き方には机械、化学、電解など様々な方法がありますが、よく使われるのはホイール磨きで、丸い布、羅紗、毛布などを何層も重ねて車輪状に縫い、研磨机の軸に取り付けて回転させて磨きます。ポリッシュホイールのキャリアの種類は多くて、綿、麻、毛、紙、革、プラスチックとその混合物などがあります;研磨材は粒が均一に細く、形が多角形で刃先が鋭いです。よく使われる研磨粉の種類、性能、用途は表2-1の通りです。研磨粉を研磨ホイールに接着剤で貼り付けます。ダイヤモンド、酸化鉄研磨粉、酸化クロム研磨粉、または半固体または液状の研磨剤を使用します。
二、膜の処理を転化します
転化膜の処理はワークをいくつかの溶液の中に浸すことで、一定の条件下でその表面に1層の緻密な保護膜を発生させて、ワークの腐食防止の能力を高めて、装飾の役割を増加します。一般的な変換膜処理には酸化処理とリン化処理があります。
(一)酸化処理です
鋼の酸化処理鋼の酸化処理は鋼部品を空気—水蒸気または化学薬品の中で適切な温度に加熱して、その表面に1層の青色(または黒色)の酸化膜を形成させて、鋼の耐食性と外観を改善します。このようなプロセスは酸化処理と呼ばれ、また発色藍処理と呼ばれます。酸化膜は緻密で丈夫なFe3O4薄膜です。厚さは0.5~1.5mmしかなく、鋼部品の寸法精度に影響はありません。酸化処理後の鋼部品はさらに石鹸液浸漬処理と油浸処理を行い、酸化膜の腐食防止能力と潤滑性能を向上させます。鋼の酸化処理には、以下の基本的なプロセスがあります。酸化処理中に溶液中の酸化剤含有量が高ければ高いほど、酸化膜を生成するスピードも速くなります。溶液中のアルカリの濃度は適当に増大して、酸化膜の厚さを得て増大して、アルカリ含有量は低すぎて、酸化膜は薄くてもろくなります。溶液の温度を適度に上げることで酸化の原因密度を高めることができます。ワークの炭素含有量が高いほど酸化しやすくなり、酸化時間が短くなります。酸化処理時間は主に鋼部品の炭素含有量とワーク酸化要求によって調整します。酸化処理プロセスは部品の精度に影響しないで、よく計器、計器、工具、銃器といくつかの机械部品の表面に使用して、それに摩耗、耐食性と保護と装飾の目的を達成させます。
アルミニウムとその合金の酸化処理アルミニウム(またはアルミニウム合金)は、自然条件下では緻密な酸化膜を生成しやすく、空気中の水分や有害なガスによる酸化や侵食を防ぐことができますが、アルカリ性や酸性の溶液では腐食しやすくなります。アルミニウムやアルミ合金の表面に保護酸化膜を得るためには、酸化処理を行うべきです。一般的な処理方法として、化学酸化法と電気化学酸化法があります。化学酸化法はアルミニウム(またはアルミ合金)の部品を化学溶液に溶かして酸化処理を行うことで強固な酸化膜を得ます。厚さは0.3 ~ 4mmです。処理溶液の性質によってアルカリ性と酸性溶液酸化処理することができます。例えば、アルカリ性酸化液はNa2CO3(50 g/L)、Na2CrO4(15 g/L)、NaOH(25 g/L)で、処理温度:80 ~ 100°C、処理時間:10 ~ 20minです。酸化処理されたアルミニウムの表面は0.5 ~ 1mmの厚さの黄金色の酸化膜を呈します。この方法はアルミニウム、アルミニウムマグネシウム、アルミニウムマンガン合金に適しています。化学酸化法は主にアルミニウムとアルミニウム合金の耐食性と耐摩耗性を高めるために使われます。また、この工法は操作が簡単で、コストが安く、大量生産に適しています。電気化学酸化法は電解液中にアルミニウムとアルミ合金の表面に酸化膜を形成させる方法で、陽極酸化法とも言います。アルミニウム(またはアルミ合金)を陽極とした工作物を電解液中に置き、通電後に陽極上に酸素を発生させ、アルミニウムやアルミ合金を化学または電気化学的に溶解させ、その結果、陽極の表面に酸化膜を形成します。陽極酸化膜は優れた力学的特性と耐食性だけでなく、強い吸着性を持っており、異なる着色方法を採用した後、さまざまな異なる色の装飾外観を得ることができます。アルミニウムとアルミニウム合金の表面で異なる性質の酸化膜を得るために、多くの場合、異なる種類の電解液を使用して実現します。一般的な電解液には硫酸、クロム酸、シュウ酸などがあります。アルミニウムとアルミニウム合金酸化処理の基本プロセスは次のとおりです。陽極酸化膜の多孔構造と強い吸着性のため、表面が汚染されやすく、特に腐食媒体が人孔に入って腐食を引き起こしやすい。そのため陽極酸化膜が形成された後、必ず閉鎖処理を行って、酸化膜の穴を閉じて、耐蝕、絶縁と摩耗などの性能を高めて、不純物や油汚れに対する吸着を弱めます。よく使われる閉じ方には、蒸気閉じ方やパラフィン、油、樹脂閉じ方などがあります。
(二)リン化処理です
リン酸塩を主とする溶液に鋼部品を浸してその表面に沈着させ、水に溶けない結晶型リン酸塩の転化膜を形成する過程をリン化処理といいます。リン化処理溶液はリン酸マンガン鉄塩とリン酸亜鉛溶液が一般的で、リン化処理後のリン化膜厚は一般に5 ~ 15mmで、その抗腐食能力は発青処理の2 ~ 10倍です。リン化膜と基体の結合力が強くて、よい防食能力と高い絶縁性能があります。大気、油類、ベンゼンとトルエンなどの媒体の中でよい耐食能力があります。油、ろう、顔料と漆などに対してすぐれた吸収力があります。しかし、リン化膜自体の強度、硬度が低く、一定の脆性があります。鋼の変形が大きい時、細かいひび割れができやすく、沖撃に耐えられません。酸、アルカリ、海水及び水蒸気の中で耐食性が悪いです。リン化処理後に表面浸漆、浸油処理を行い、耐蝕能力を大きく向上させることができます。リン化処理に必要な設備は簡単で、操作が容易で、コストも安く、生産効率も高いです。一般的な机械設備では鉄材料の部品の防護層として、また各種兵器の潤滑層や防護層として使用されます。
(三)電気めっきと化学めっき
めっきめっきは、メッキされた製品を陰極として直流電流を印加し、金属塩溶液の陽イオンをワーク表面に沈着させてめっき層を形成します。めっきは実質的に電気分解プロセスであり、陰極に析出した物質の重さは電流の強さと時間に比例します。めっきを行うために必要な三つの条件は,電源,水槽(液)及び電極です。めっきは、材料の保護または装飾の目的を達成するために、その表面特性と外観を変更するために、材料または部品のより均一で、良好な結合力を有するめっき層をカバーすることができます。メッキに加えて、美しく、耐久性のある製品だけでなく、特別な机能を取得することができ、金属製品の耐食性、耐摩耗性、耐熱性、反射性、導電性、潤滑性、表面硬度を向上させることができ、摩耗部品のサイズや表面欠陥を修復する半導体デバイス上でメッキは、非常に低い接触抵抗を得ることができます;電子部品の上でアルミニウム-錫合金をめっきしてとても良いロウ付け性能を獲得することができます;ピストンリングと軸にクロムメッキを施すことで高い耐摩耗性を得ることができます。局所的な炭素浸透を防ぐ銅メッキ、局所的な窒素浸透を防ぐ錫メッキなどです。現在では、銅メッキ、ニッケルメッキ、クロムメッキ、亜鉛メッキ、銀メッキ、メッキなどの技術が広く使用されています。
化学めっき化学めっきは外付け電源なしとも言います。M2+ + 2e→Mすなわち溶液中に2つの正価電荷を帯びた金属イオンMが存在し、2つの電子を受けて金属原子Mに変化し、適切な条件下でワークの表面に沈着してコート層を形成します。化学めっきによって得られる電子は化学反応によって直接溶液中に生成され、一般的に電荷交換堆積、接触堆積、還元堆積などいくつかの種類があります。現在、化学ニッケルメッキ、銅メッキ、銀メッキ、金メッキ、コバルトメッキ、パラジウムメッキ、プラチナメッキ、錫メッキなどが工業生産に用いられており、特に電子工業に広く用いられています。
表面処理の応用に関する一般的な知識です
詳しく表訪問してください:http://www.josen.net/steel-knowledge/1602812850.htmlページを閲覧できる。
ステンレス表面処理
ステンレス鋼は独特の強度、高い耐摩耗性、優れた防腐性能、錆びにくいなどの優れた特性を持っています。だから広く化学工業業界に応用して、食品机械、机電業界、環境保護業界、家庭電器業界と家庭装飾、装飾業界、人々に華麗で高貴な感じを与えます。
ステンレスの応用は今後ますます拡大していくと思われますが、ステンレスの応用の発展は表面処理技術の発展に大きく左右されます。
1ステンレス鋼の一般的な表面処理方法です
1.1ステンレス品種の概要です
1.1.1ステンレス鋼の主要な成分:一般的にクロム(Cr)、ニッケル(Ni)、モリブデン(Mo)、チタン(Ti)などの良質な金属元素を含んでいます。
1.1.2一般的なステンレス鋼:クロムステンレス鋼、Cr≧12%以上を含みます;ニクロムステンレス鋼は,Cr≧18%,Ni≧12%を含みます。
ステンレスから1.1.3金相組織構造分類:オーステナイトステンレス、例えば:1Cr18Ni9Ti, 1Cr18Ni11Nb, Cr18Mn8Ni5があります。マルテンサイト系ステンレス鋼Cr17 Cr28などです一般的に非磁性ステンレス鋼と磁性を帯びたステンレス鋼と呼ばれます。
1.2ステンレス鋼の一般的な表面処理方法
ステンレス鋼の表面処理技術を常用して以下のいくつかの処理方法があります:①表面の白色化処理;②表面鏡面の光沢処理です。③表面の着色処理です。
1.2.1表面の色の白化処理:ステンレス鋼は加工過程の中で、板を巻くことを経て、端を刺して、溶接あるいは人工の表面の火焼加温処理を経て、黒い酸化皮を発生します。このかたい灰黒色の酸化皮は主にNiCr2O4とNiFの二種類のEO4成分で、以前はフッ酸と硝酸による強い腐食方法で除去するのが一般的でした。しかし、この方法のコストは大きく、環境を汚染し、人体に有害で、腐食性が大きく、徐々に淘汰されます。酸化皮の処理方法は主に2つあります。
.ブラスト(丸)法:主にマイクロガラスビーズを噴射する方法で、表面の黒い酸化皮を除去します。
古代の化学法:1種の汚染されていない酸洗の鈍化膏と常温無毒の無机添加剤の洗浄液を使用して浸洗を行います。これによりステンレス色の白化処理の目的を達成します。処理するとほとんど光のない色に見えます。この方法は、大型で複雑な製品に適しています。
1.2.2ステンレス鋼の表面鏡面光沢処理方法:ステンレス製品の復雑な程度とユーザーの要求状況に応じて、それぞれ机械研磨、化学研磨、電気化学研磨などの方法で鏡面光沢を達成することができます。これら3つの方法のメリットとデメリットは次の通りです。
1.2.3表面の着色処理:ステンレス鋼の着色だけでなく、ステンレス鋼製品の色の種類を増やすだけでなく、製品の耐摩耗性と耐腐食性を向上させます。
ステンレスの着色方法には次のようなものがあります。
化学酸化着色します;
古代に云う電気化学酸化着色法;
イオン酸化物の着色法を堆積します;
中高温酸化着色法;
例:気相分解着色法です。
それぞれの方法の簡単な概要は次の通りです。
化学酸化着色法:特定の溶液において化学酸化によって膜の色が形成されるもので、二クロム酸塩法、混合ナトリウム法、硫化法、酸性酸化法及びアルカリ性酸化法がある。一般的に「インコ法」(INCO)が多く使われますが、一ロットの製品の色味が一致することを保証したいなら、必ず参比電極で制御しなければなりません。
古代に雲う電気化学着色法:特定の溶液の中で、電気化学酸化によって膜の色を形成します。
⑶イオン蒸着酸化物着色法化学法:ステンレスのワークを真空コート机の中で真空蒸発めっきします。例えば、チタンメッキのケースやストラップは、黄金色が一般的です。この方法は大量生産品の加工に適しています。投資が大きく、コストが高いため、小ロットの製品は採算が合わないからです。
中高温酸化着色法:特定の溶融塩の中で、ワークを一定の工程パラメータに浸入して保持することで、ワークに一定の厚さの酸化膜を形成させて、様々な異なる色味を示すものである。
例:気相分解着色法:復雑,工業での応用は少ないです。
1.3処理方法の選択です
ステンレス鋼の表面処理はどの方法を選んで処理するかによって、製品の構造、材質、及び表面に対して異なる要求、適切な方法を選んで処理します。
2ステンレス部品のサビの原因としてよくあることです
2.1化学的腐食です
2.1.1表面汚染:油汚れ、ほこり、酸、アルカリ、塩などのワークの表面に付着して、一定の条件で媒体を腐食することに変換して、ステンレス鋼の部品の中のいくつかの成分と化学反応を起こして、化学腐食と錆びます。
2.1.2表面に傷をつける:ステンレス鋼の保護能力を低下させるため、不鈍化膜の破壊の様々な傷は、化学媒体と反応しやすく、化学腐食と錆びを発生します。
2.1.3洗浄:酸洗浄は鈍化した後に洗浄しないで残液が残って、直接ステンレス鋼の部品を腐食します(化学腐食)。
2.2電気化学的腐食です
2.2.1炭素鋼の汚染:炭素鋼の部品の接触による傷と腐食媒体を形成して原電池の電気化学腐食が発生します。
2.2.2カット:スラグ、スプラッシュなどのさびやすい物質の付着とメディアを腐食し、電気化学的な腐敗を発生します。
2.2.3焼校:火炎加熱区域の成分と金相組織が変化して均一ではなくて、腐食媒体と形成して原電池の電気化学腐食が発生します。
2.2.4溶接:溶接領域の物理的欠陥(エッジ噛み、気孔、割れ、溶解していない、完全に溶接していないなど)と化学的欠陥(結晶粒、貧クロム、偏析など)と腐食媒体を形成して原電池の電気化学的腐食が発生します。
2.2.5材質:ステンレス鋼の化学的欠陥(成分が均一でない、S、P不純物など)と表面の物理的欠陥(粗しょう、砂目、ひび割れなど)に有利に腐食媒体と原電体を形成して電気化学的腐食が発生します。
2.2.6鈍化:酸洗の鈍化効果は、不均一または薄いステンレス鋼の表面の不鈍化膜をもたらし、電気化学的腐食を形成しやすいです。
2.2.7洗浄:酸洗浄の残留は鈍化残液とステンレス鋼の生成物とステンレス鋼の部品の電気化学的腐食を形成します。
2.3応力集中は応力腐食を引き起こしやすいです
要するに、ステンレス鋼はその特殊な金相組織と表面の鈍化膜により、一般的に誘電体と化学反応して腐食しにくいのですが、いかなる条件の下でも腐食できないわけではありません。腐食媒体と誘因物(例えば傷、飛び散り、割れ目など)が存在する条件下では、ステンレス鋼も腐食媒体とゆっくりとした化学と電気化学反応で腐食することができます。また、一定の条件下では腐食速度がかなり速いため、サビ現象が発生します。特に点腐食と継ぎ目腐食です。ステンレス部品の腐食メカニズムは主に電気化学的腐食です。
そのため、ステンレス製品は加工作業の過程ですべての有効な措置を取るべきで、できるだけ錆の条件と誘因の発生を避けます。実際には、多くの錆の条件と誘因(例えば傷、飛び散り、割滓など)は、製品の外観品質にも著しい不利な影響を与え、克服しなければなりません。
3ステンレス製品の加工に問題があります
3.1溶接の欠陥:溶接の欠陥はより深刻で、手の机械を使って処理方法を研磨して補完しにきて、生じた研磨の跡、表面の不均一をもたらして、美観に影響します。
3.2表面は一致していません:溶接だけ酸洗を行って鈍化して、表面の不均一をももたらして、美観に影響します。
3.3傷を除去するのは難しい:全体の酸洗浄は鈍化してもできませんし、加工過程で発生した各種の傷を取り除くことができません。また、傷を取り除くことができません。飛び散る溶接のため、ステンレス鋼の表面に付着した炭素鋼、飛び散るなどの不純物が、媒体を腐食する条件で生化学的腐食または電気化学的腐食によって錆びます。
3.4研磨して研磨して研磨して研磨した後に酸洗の鈍化処理を行って、面積の大きいワークに対して、均一に一致した処理効果を達成することが困難で、理想的な均一な表面を得ることができません。また工数費用、副資材費用も高くなります。
3.5酸洗能力は限られています:酸洗鈍化膏は万能ではありませんて、プラズマ切断、火炎切断産と黒い酸化皮、除去しにくいです。
3.6人為的な要因による傷がより深刻です:弔り上げ、輸送や構造加工の過程で、打撲、引き延ばす、ハンマーなどの人為的な要因による傷がより深刻で、表面処理が難しくなるだけでなく、処理後の錆の主な原因です。
3.7設備の要因:型材、板材の巻曲がって、曲がっている過程の中で、傷と折り目の処理の後に錆の主な原因を発生することをもたらします。
3.8その他の要因:ステンレス素材の調達、貯蔵の過程で、弔り上げ、輸送の過程で生じる打撲や傷も比較的深刻で、錆の原因の1つです。
4予防措置を取るべきです
4.1貯蔵・弔り上げ・輸送
4.1.1ステンレス鋼の部品の貯蔵:専用のラックがなければならなくて、ラックは木製または表面塗装の炭素鋼の橋台またはクッションにゴムで敷いて、炭素鋼などの他の金属材質と隔離します。保管する時、保存位置は弔り運べやすく、他の材料保管区と相対的に隔離しなければなりません。防護措置があって、ほこり、油汚れ、鉄錆がステンレスに対する汚染を避けるべきです。
4.1.2ステンレス鋼の部品はつり下げる:つり下げる時、専用のつり具を使用しなければならなくて、例えばつり下げるベルト、専用のクリップなど、ワイヤロープを使用して表面を傷つけないようにします;また弔り上げ時や放置時に沖撃や打撲による傷を避けるようにしています。
4.1.3ステンレス鋼の部品の輸送:輸送する時、輸送机関(例えば小さい車、電気自転車など)を適用して、ほこり、油汚れ、ステンレス鋼の錆を防ぐために清潔な隔離措置があるべきです。ぐずぐず、打撲、傷つきは厳禁です。
4.2加工します
4.2.1加工区:ステンレス部品の加工区域は相対的に固定すべきです。ステンレス加工品のプラットフォームは、ゴムパッドを敷くなどの隔離措置を取る必要があります。ステンレス部品加工区の定置管理、生産を強化して、ステンレス部品の損傷と汚染を避けるべきです。
4.2.2下料:ステンレス鋼の件の下料はせん断あるいはプラズマ切断、のこぎりなどを採用します。
ってカット:カットする時、送込台と隔離し、ホッパーにもゴムパッドを敷いて、傷をつけないようにしなければなりません。
古代に雲うプラズマ切断:プラズマ切断後、スラグをきれいにする必要があります。ロット切断の時、すでに完成した部品に対して直ちに現場を掃除しなければならなくて、スラグを切って工作物に対して汚すことを避けるためです。
材料を切ります:材料を切る時、はさみにゴムを加えて保護しなければなりません。材料を切った後に工作物の上の油汚れ、残りかすなどを掃除しなければなりません。
4.2.3机械加工:ステンレス鋼の部品は車、フライスなどの机械加工の時も保護に注意しなければならなくて、作業は完成しなければならなくてきれいなワークの表面の油汚れ、鉄くずなどの雑物を掃除します。
4.2.4成形加工:板を巻いて、曲がって過程の中で、ステンレス鋼の部品の表面の傷と折り目を避ける効果的な措置を取るべきです。
4.2.5リベット溶接:ステンレス鋼の部品はペアを組む時、強制組み立てを避けなければなりません。特に火炎焼組み立てを避けます。組対または製作過程でプラズマ切断を一時的に採用する場合、割滓による他のステンレス部品の汚染を避けるために隔離措置を取るべきです。切断後、ワークの切れ端はきれいにします。
4.2.6溶接:ステンレス鋼の部品を溶接する前に、油汚れ、錆、ほこりなどを取り除く必要があります。アルゴン溶接をお勧めします。手アーク溶接の場合は小電流、速い溶接をお勧めします。非溶接区域でアークを引くことを厳禁して、アースの位置は適当で、連結は堅くて、アークの擦り傷を避けるためです。溶接時にはね防止措置(白灰を塗るなどの方法)を取ることが必要です。溶接後はステンレス鋼(炭素鋼は使用不可)のショベルを用いて、スラグや飛び散りを徹底的に除去します。
4.2.7多層溶接:多層溶接の場合、層間スラグをきれいに除去しなければなりません。多層溶接の場合、層間温度を60℃を超えないように制御します。
4.2.8溶接:溶接継手は修理しなければならなくて、溶接の表面はスラグ、気孔、噛み辺、飛び散って、ひび割れ、未溶解、未溶接などの欠陥があってはならなくて、溶接と母材は丸く遷移しなければならなくて、母材より低くてはなりません。
4.2.9マニエリスム:ステンレス鋼の部品のマニエリスムは、火炎加熱の方法を使用することを避けるべきで、特に同じ領域を繰り返し加熱することを許可しません。矯正する時、できるだけ机械的な装置を使用して、あるいは木のハンマー(ゴムのハンマー)またはクッションゴムのハンマーで、ステンレス鋼の部品を損傷することを避けるために、鉄のハンマーで打つことを禁止します。
4.2.10運搬:ステンレス鋼の部品は加工の過程で運搬を行う時、応用輸送机器(例えば小さい車、電気自転車や天車など)、ほこり、油汚れ、ステンレス鋼の鉄錆を防ぐための隔離保護措置が清潔でなければなりません。テラスや床に直接もたれかかったり、打撲や引っかき傷をつけたりすることは厳禁です。
4.3表面処理
4.3.1掃除して磨く:もし損傷があるならば研磨して、特に炭素鋼の部品と接触して傷と飛び散ることをもたらして、割滓のもたらした損傷を真剣に徹底的に掃除してきれいに磨かなければなりません。
4.3.2机械研磨:適切な研磨ツールを使用して研磨を行うには、処理が均一である必要がありますし、再傷を避けるためにドロップします。
4.3.3油を除去してほこりを取り除く:ステンレス鋼の部品は酸洗を行う前に鈍化して、工芸によって油汚れ、酸化皮、ほこりなどの雑物を除去しなければなりません。
4.3.4水サンドブラスト処理:異なる処理要件に応じて、異なるマイクロガラスビーズ、異なるプロセスパラメータを選択し、オーバースプレーなどを避ける必要があります。
4.3.5酸洗鈍化:ステンレス鋼の部品の酸洗鈍化は厳格にプロセスの要求によって鈍化しなければなりません。
4.3.6洗浄乾燥:酸洗は鈍化した後、厳密にプロセスによって中和、洗浄、乾燥、完全に残留酸液を除去する必要があります。
4.3.7保護:ステンレス鋼の部品の表面の処理が終わった後に、しっかりと保護しなければならなくて、人が油汚れ、ほこりなどの雑物の二次汚染をなでてさわらないようにします。
4.3.8再加工を避ける:ステンレス部品の表面処理後、部品または製品の再加工を避けるべきです。
含まれます:化学薬品船、タンク、パイプボイラーなどステンレス/低炭素鋼製品の表面処理、例えば研磨/研磨、酸洗浄/不鈍化、検査/監督、技術コンサルティングなど。
主なサービス対象は船舶、石油化学、食品設備などです。
プラスチック表面処理技術です
プラスチックの加工や改質技術の向上に伴い、応用分野が急速に広がっています。プラスチックの表面装飾、材料保護、性能の改善などのアプリケーション分野はますます増加しているが、さまざまなプラスチック材料の構造と組成物は、対応する表面性能にも明らかな違いがあります。用途に応じたさまざまな表面処理技術や製品が登場しています。
プラスチックの表面に適応します
必要に応じて,復数の処理技術が開発されています。一般的な技術は、溶剤洗浄(脱脂)、コロナ処理、短波紫外線放射処理、サンドペーパー処理、サンドブラスト処理、プラズマエッチング、化学エッチング、加熱処理などです。材料によって取り扱い方が異なることはよくあります。
表面処理方法の選択です
ほとんどのプラスチックは表面が低いため、装飾、印刷、塗装などの多くの処理方法はそのままでは適用できず、まず表面処理を行う必要があります。プラスチックと様々な異なる材料との接着性は表面処理の重要な課題の1つです一般的にプラスチックの接着性は材料の構造や組成に関系します。
構造的な影響です
PPやPEなどのポリオレフィン材料は、表面エネルギーが非常に低く、通常30-34ダインしかありません。良好な接着を実現するには、一般的に表面が40ダインを下回らないことが求められます。接着試験によると、PEはプラズマ処理後に接着強度を10倍に高めることができます。クロム酸処理を施すと,接着性が約5倍向上します。同様の処理をすると,PPの接着強度はイオン化処理で約200倍,クロム酸処理で約600倍になります。
なぜcr酸はPPには効果があり、PEには効果があるのでしょうか。これはPP鎖の炭素原子それぞれがメチル基(-CH3)を1つずつ持っているからです。メチル基は酸素イオン化またはクロム酸処理を経た後にカルボキシ基によって極めて酸化されやすくなります。また、メチル基がわずかに酸化されても、カルボキシ基の存在によりPPの接着性や極性が著しく改善します。PEにはそれがありません。ポリマーの化学構造は、表面処理を行う際に考慮しなければならない重要な要素であることがわかります。
成分の影響です
様々な混合物や共重合物の場合、材料成分も表面処理方法の選択に影響を与えます。例えばフッ素ポリマーとその共重合体の表面エネルギーはポリオレフィンよりも低く、典型的な範囲は18-26ダインです。PTFEのような高フッ素含有樹脂では,エポキサン酸ナトリウムをエッチングすると接着性が10倍になりますが,酸素やプラズマ・アルゴン処理すると3倍になります。PEの傾向は、これとは正反対です。
しかしながら,フッ素樹脂とPEの共重合体は,プラズマ処理やシクロキサン酸ナトリウム処理でいずれも10倍の接着性になります。プラズマ処理はPEにより多く作用し、シクロキサン酸ナトリウム処理はフッ素樹脂により主に作用することがわかります。このことから、異なる材料を共重合させることで、材料の処理性を改善できることがわかりました。異なる成分の共集合物についても、材料の特性に応じて処理方法を選択する必要があります。
選び方のテクニック
異なる処理方法は異なるポリマー構造と組成に影響を与えますので、表面処理方法の選択も材料の構造と組成に基づいて行うべきです。低表面能プラスチック(<35ダイン)は、主に経験によります。高表面プラスチックは、それ自体が良好な接着性を持っているので、ほとんどすべての処理方法に適しています。一般的に、プラスチックは表面エネルギーが低ければ低いほど多くの処理を必要とします。しかし、一部のポリマーは低い表面エネルギーを持ち、溶剤(ABS、PC、PS、AC、PVCなど)で直接接着することもできます。実際、ACの接着が可能なのは、多くのアクリル接着剤自体が溶剤作用を持っているからです。一方、POM、PPO、PPS、およびベンゼン環を含む他のポリマーのような抗溶剤材料については、通常、表面の酸化処理または毛の除去が必要です。ポリアミンやポリイミドのような接着がより困難な材料の接着には、一般的に表面エッチングが必要です。
極性を持つプラスチック(例えば、ポリエステル、エポキシ、ポリウレタン、ポリアミンなど)については、表面処理の方法が異なります。一般的に極性が小さいほど、必要な処理は少なくなります。これらの中で極性が最も強いのはポリエステルとエポキシで、表面に毛を打って接着します。剛性ウレタンは極性が高くないため、通常はウレタン接着剤で接着できますが、エポキシによる表面処理が必要です。ポリアミンはその中でも極性が最も小さく、処理せずに接着することができます。
実際の処理の過程に対して、通常更に加工の経済性を考慮して、より実際の加工の需要に合うようにします。加工時間、温度、露出度、乾燥条件など、一般的に関与するさまざまなプロセスパラメータを注意深く考慮する必要があります。処理方法を選択するとき、対応する材料の化学的特性、ポリマー鎖段構造、および応用分野の特殊な要件を総合的に考慮する必要があります。高い依存性の接着は通常より多くの表面処理を必要とします。
表面処理の応用技術です
メーカーが製品の品質をますます高く要求するにつれて、作業環境を改善し、作業効率と処理信頼性を向上させるための配合技術と材料が開発され、市場応用も広がってきた。
熱分子結合加工技術です
FTS社はプラスチック塗装前処理装置を製造する専門会社です。同社は熱分子接着加工技術(AtmaP)を開発し、材料の接着性を改善して品質を向上させ、環境にも優しい技術を開発しました。AtmaP技術の実現はCirqualバーナの採用により実現しました。AtmaP加工は主にアルケン系プラスチック制品の表面に化学カップリング剤を組み合わせて接着性を改善します。サークルバーナから供給される燃焼炎は、カップリング剤をプラーク表面に拡散させる唯一の動力です。燃焼器は軽量アルミニウム構造で、メンテナンスと操作が迅速にでき、特に自働処理に適しています。この製品は主に塗装、接着、装飾、層合、印刷またはテープで材料を接着する表面処理に適しています。現在採用されている他の類似プロセスでは,AtmaPの効果は得られていないと説明しています。
光硬化塗料は自動車用プラスチックに使われています
自動車部品の多くには、エンジニアリングプラスチックやポリマー複合材料が採用されていますが、塗料で表面の性質を改善するだけでなく、場合によっては材料の性能を向上させることができます。自動車のグローブやミラーミラーの材料をガラスの代わりにプラスチックにすることは、光硬化塗料の処理技術に役立ちます。ポリカーボネートは成型加工がしやすく、軽量でフレキシブルで壊れにくいという長所がありますが、表面強度が足りず、傷や擦れに弱い上に耐候性が悪く、黄色くなりやすい。光固化塗料を採用してその表面性質を改善します。塗装時間を大幅に節約できるだけでなく、コーティングにも優れた光学耐擦性があり、長期耐侯性要求を満たすことができます。新しい技術のおかげで、今ではポリカーボネイト製のグローブがほぼ完全にガラス製のグローブに取って代わられています。
自動車用ミラーもプラスチック製ですが、高い反射性能が求められます。この目的を達成するために、プラスチックの表面を3回紫外照射する必要があります。まずプラスチックは紫外照射を経て表面に光化学反応を生じさせて表面張力を増加させて、光固化塗料の流平と付着に有利です;塗布光硬化ワニス硬化によりプラスチック表面が平坦になり金属化しやすくなります
キーワードです:联合国,志源电池厂
関連情報です
2018-11-23
2018-10-12
2022-04-06
2012-01-07
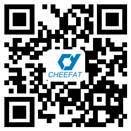
Copyright © 2023 志源表面処理(恵州)有限会社 All Rights Reserved 粤ICP备2021109730号 技術サポート:中国企業のパワーです 恵州 SEO